Overview:
The silicone shower head is a vital accessory for contemporary bathrooms, available in round, square, and single nozzle designs. Known as silicone replacement spray nozzles or rainfall showerheads, these products offer versatility and convenience. Made from food-grade silicone, they are clog-resistant and require minimal maintenance—typically just a quick wipe to remove limescale. Capable of withstanding temperatures from 0 to 90 degrees Celsius and compatible with water pH levels between 5 and 9, our shower nozzles are crafted using precision compression molding and stringent quality control measures. This ensures durability and reliable performance, making them an excellent choice for any bathroom setting.
Features:
Service Specifications | Details |
Service | OEM |
Part Material | Silicone or rubber (NR, NBR, SBR, BR, IR, CR, EPDM, IIR, FKM, SIR, PU, ACM, CO, etc.) |
Material Hardness | Silicone: 20–90 Shore A; Rubber: 20–90 Shore A |
Color | Customized according to Pantone colors |
Appearance | As per customer requirements |
Drawings | Acceptable in 2D or 3D formats |
Temperature Resistance | 0–90 degrees Celsius |
Tolerance | ±0.05 mm |
Technology | Hot compression molding or injection molding |
Quality Control | Internal QC control |
Food Grade Material | FDA or LFGB compliant |
MOQ | Small orders accepted |
Package | Customized per customer request |
Trade Terms | Ex-works; FOB Xiamen; CIF |
Payment Terms | Sample mold: 100% prepaid; MP Mould: 50% deposit via T/T in advance, balance 50% after sample approval |
Specifications | Compliant with ISO 9001 and ROHS Directive for Green Products |
Production Process:
- Design and Engineering: The production process begins with the creation of detailed designs and specifications using advanced CAD software. Engineers develop 2D and 3D models to ensure precise dimensions and optimal functionality.
- Material Selection: We select high-quality food-grade silicone known for its durability, temperature resistance, and chemical stability, ensuring that the final product adheres to industry standards.
- Molding Process: The chosen silicone undergoes either hot compression molding or injection molding, based on the specific design requirements. This involves heating the silicone and placing it into molds to form the desired nozzle shape.
- Curing: Post-molding, the silicone components are cured to enhance their strength and stability. This typically involves heating the molded parts in an oven to achieve the required hardness.
- Finishing and Quality Control: The nozzles then go through finishing processes, including trimming and surface smoothing. Each product undergoes rigorous quality control checks to ensure it meets specifications and performance standards.
- Testing: Functional tests are conducted to evaluate the nozzle’s performance, focusing on water flow and leak resistance. This step verifies that the product fulfills all operational criteria.
- Packaging: Finally, the silicone shower nozzles are packaged according to customer specifications, ensuring safe transport and delivery.
Why Choose Us?
- Direct Manufacturer Pricing: Enjoy cost-effective solutions sourced directly from the manufacturer, ensuring outstanding value.
- Expert Team: Our team consists of five skilled R&D engineers, experienced production staff, and dedicated quality control professionals, all focused on delivering premium products.
- Cutting-Edge Molding Facilities: Our advanced molding plants allow for rapid tooling production, ensuring timely delivery of qualified samples and finished products.
- Controlled Manufacturing Environment: We maintain a dust-free production environment to uphold the highest cleanliness standards in silicone rubber manufacturing.
- Sustainable Materials: We use eco-friendly materials that meet ROHS, SGS, ISO, FDA, and LFGB certifications, guaranteeing safe and sustainable products.
- Tailored OEM Solutions: Our comprehensive OEM services are designed to accommodate your specific design and production needs, offering flexibility and customization for your unique requirements.
Quality Test Process:
Our quality control process for silicone gasket shower nozzles employs cutting-edge equipment to uphold the highest quality standards. We utilize a Coordinate Measuring Machine (CMM) for accurate dimensional assessments and an Optical Comparator for detailed profile inspections. A Durometer is used to measure material hardness, while leak testing equipment ensures the integrity of seals. Our Water Flow Test Apparatus evaluates performance under real operational conditions, and a Temperature and Humidity Chamber simulates various environments to assess durability. Additionally, trained personnel perform thorough visual inspections to identify surface defects and ensure color consistency. This comprehensive testing regimen ensures that each nozzle meets rigorous functional and aesthetic criteria.
Factory Show:
Thesun Industry operates in a spacious 4,500㎡ facility and boasts over 20 years of OEM experience. Our factory is equipped with world-class processing machinery, including Roders, Makino, Sodick, and YCM, enabling us to achieve micron-level precision in tooling manufacturing. Utilizing advanced equipment such as ARBURG, Miltitech, and 2KM, we can produce ultra-precision products with weights as low as 0.02g and thicknesses down to 0.1mm. Additionally, our ISO-certified Class 8 medical dust-free workshop ensures a reliable manufacturing environment for medical device components, maintaining the highest standards of cleanliness and precision.
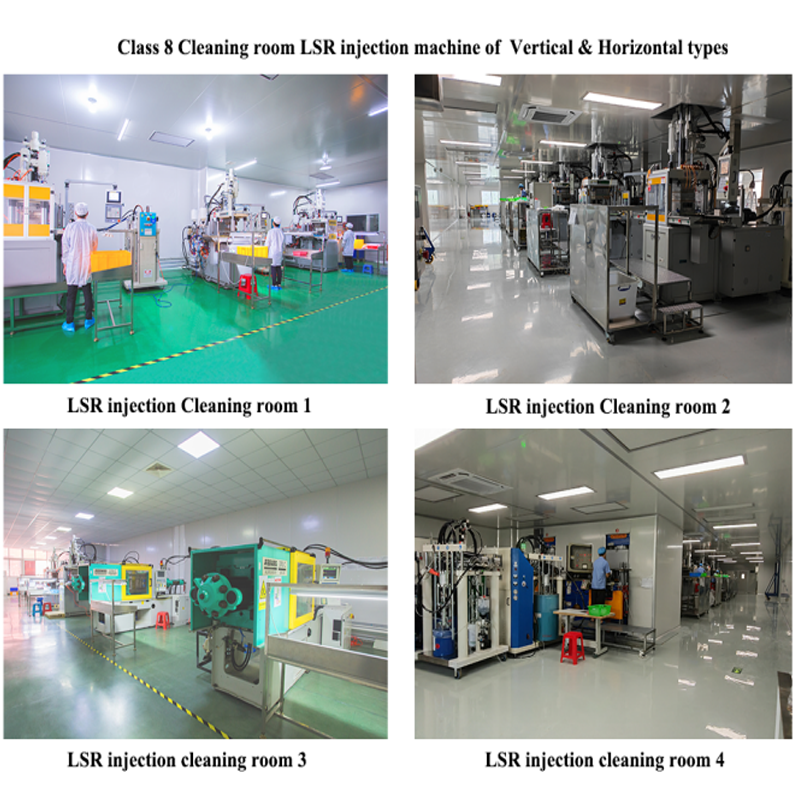