CNC Milling Service
Experience precise and efficient CNC milling services for your custom part needs. Send us your inquiries today for top-quality results and quick turnaround times.
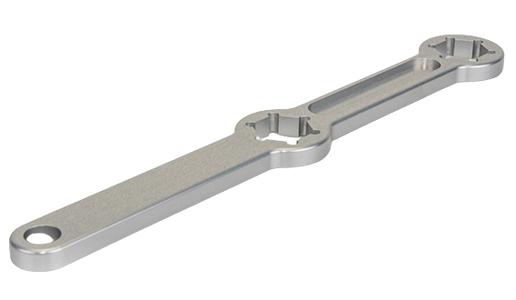
Certifications
ISO 9001:2015 | AS9100D
About CNC Milling
CNC milling refers to the process of using computer numerical control (CNC) machines to remove material from a workpiece using rotary cutters. A computer program controls the movement of the milling machine and its cutting tools, following G-code instructions to shape the final part.
How CNC Milling Works
CNC mills are highly proficient at profile cutting harder materials. Like all CNC machines, they rely on G-Code to operate, which is generated through CAM software. The G-Code provides precise instructions to the machine, dictating the tool head's movement, rotational speed, cutting depth, workpiece positioning, and other crucial factors such as speed, feed rate, and coordination. The complexity of the G-Code depends on the number of axes the milling machine possesses.
While CNC mills can still be utilized for profile cutting softer materials, they are not as cost-effective as CNC routers for this purpose. The primary distinction between these machines lies in how they handle the cutting process. CNC routers keep the workpiece stationary while directing the cutting head around it, whereas CNC mills may move both the tool head and the workpiece. As a result, CNC mills are predominantly employed in industrial manufacturing, while CNC routing is more common in lower output manufacturing, particularly for tasks involving woodworking.
CNC milling offers several advantages over manual milling, including improved accuracy, repeatability, and the ability to produce complex geometry. It is widely utilized in industries such as automotive, aerospace, electronics, and prototyping for manufacturing parts with high accuracy and efficiency.
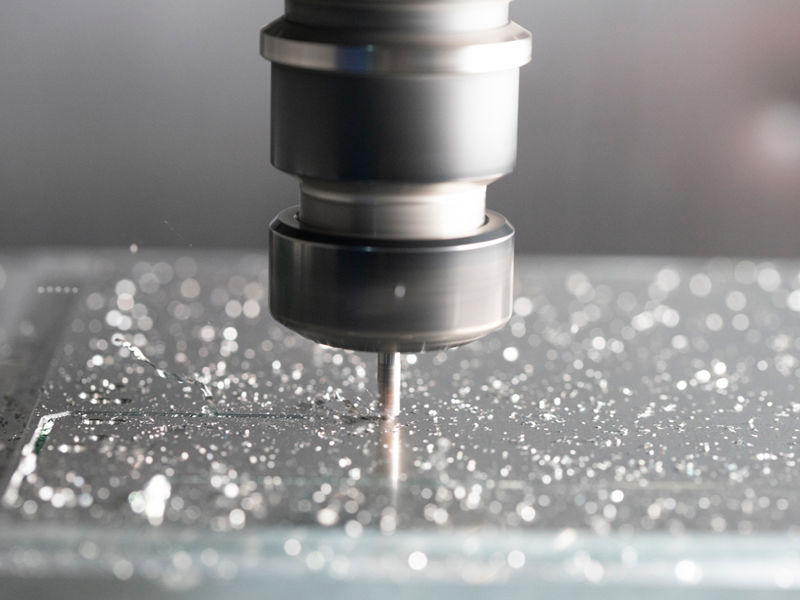
Our Custom CNC Milling Service
Advantages of ThesunIndustry’s CNC Milling Service
We are committed to providing you with high-quality custom CNC milling services no matter the scale of your project. Our goal is to be your trusted partner, working together to achieve project success and growth.
Advanced CNC Milling Machines: We utilize high-performance CNC milling machines with multi-axis linkage capability, enabling simultaneous cutting in multiple directions and achieving high-precision machining for complex parts.
High-Precision Cutting Tools: Equipped with high-precision cutting tools, we achieve micro-level precision machining, ensuring each workpiece meets stringent dimensional and surface quality standards.
Advanced Control System: Leveraging advanced CNC technology, we achieve precise control over tool positions and movements, enabling the machining of complex shapes and intricate details.
CAD/CAM Software: Our team uses advanced CAD/CAM software for design and programming, swiftly generating machining paths to enhance production efficiency.
Inspection Equipment: Equipped with advanced inspection devices, including coordinate measuring machines and spectrometers, we conduct comprehensive quality inspections to ensure each workpiece meets strict quality standards.
Professional Technical Team: With our experienced technical team proficient in CNC machining, we offer customized solutions tailored to specific customer requirements.
Reliable CNC Milling Solutions
At Lingshan Tech, we have full capacity workshops and machines capable of CNC milling, supporting 3-axis, 4-axis, 5-axis, and right angle milling capabilities. Whether you need simple straight lines or intricate geometric shapes, we offer instant pricing, on-demand lead times, and design-for-manufacturability(DFM) feedback for your custom CNC milled parts. No matter what your industry, you can rely on Lingshan Tech to meet your CNC milling needs.
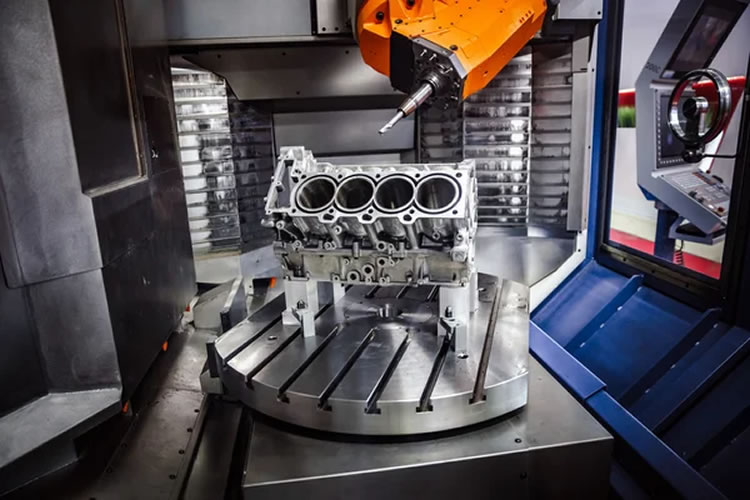
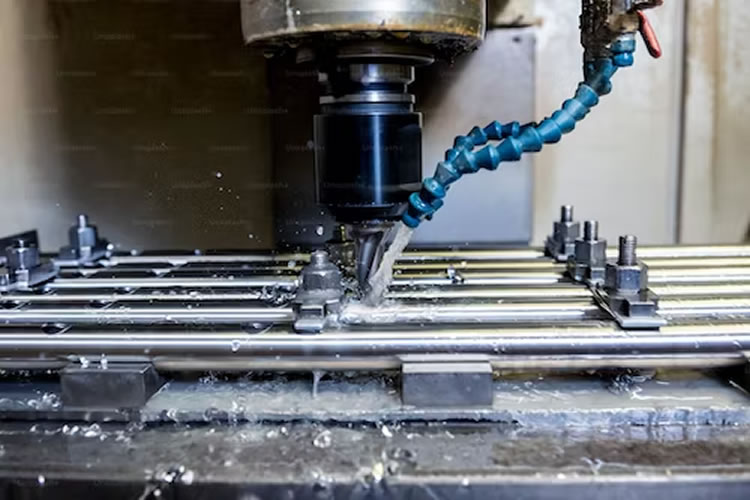
Fast Prototyping & Efficient Production
Lingshan Tech offers fast prototyping and efficient production with diverse surface treatments, ensuring timely delivery of high-quality CNC milled parts. Adhering to ISO 9001 standards, our experienced team provides personalized support for design, materials, and project needs. Trust us as your reliable partner for tailor-made CNC milling solutions and enhanced product quality.
Material
We stock more than 30 production-grade plastic and metal materials that are suitable for various part applications and industries.
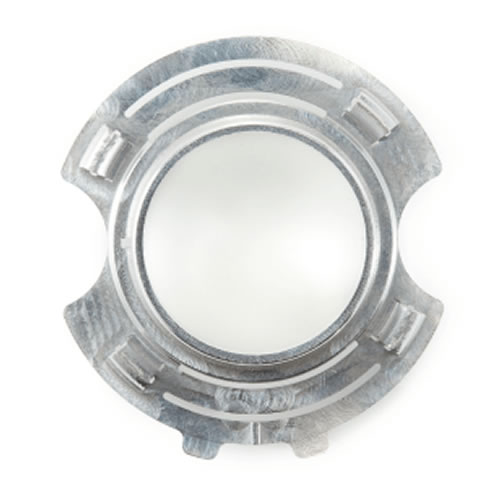
Plastics
|
|
Metals
- Aluminum
- Brass
- Copper
- Stainless Steel
- Steel Alloy
- Steel Mild Low Carbon
- Titanium
Anodizing and Chromate Plating Specifications
Anodize | Hard Anodize | Chromate |
---|---|---|
MIL-A-8625 Type II, Class 2 (Blk)
MIL-A-8625 Type II, Class 1(Clr) |
MIL-A-8625 Type III, Class 2 (Blk) | MIL-DTL-5541 Type II, Class 3 (Clr) |
CNC Milling Tolerances & Standards
Description | General Tolerance or Standard |
Maximum Part Size | Milled parts up to 80” x 48” x 24” (2,032 x 1,219 x 610 mm). |
Distance Dimensions | For features of size (Length, width, height, diameter) and location (position, concentricity, symmetry) +/- 0.005”. |
Orientation and Form Dimensions | 0-12" +/- 0.005", Angularity 1/2 degree. For 24" and beyond please consult Xometry's Manufacturing Standards. |
Precision Tolerances | Xometry can manufacture and inspect to tight tolerances per your drawing specifications including GD&T callouts. |
Minimum Feature Size | 0.020” (0.50 mm). This may vary depending on part geometry and chosen material. |
Threads and Tapped Holes | Xometry can accommodate any standard thread size. We can also machine custom threads; these will require a manual quote review. |
Surface Finish | The standard finish is as-machined: 125 Ra or better. Additional finishing options can be specified when getting a quote. |
Edge Condition | Sharp edges will be broken and deburred by default. Critical edges that must be left sharp should be noted and specified on a print. |
Available Finishes
ThesunIndustry's CNC milling surface finishes encompass a variety of methods aimed at optimizing the surface quality and characteristics of the parts. We carefully select and apply suitable surface finishing methods based on specific customer requirements and project needs. Our commitment is to provide high-quality CNC milling services, catering to various industries, and continuously innovating and optimizing surface finishing techniques to ensure customer satisfaction and product competitiveness. Here are some common CNC milling surface finishes provided by ThesunIndustry:
Polishing
We use abrasives or grinding tools to polish the surface of the parts, achieving a smooth and bright appearance. Polishing removes surface defects and burrs, enhancing surface smoothness and luster.
Grinding
Using grinding wheels, we perform grinding on the surface of the parts to achieve higher flatness and dimensional accuracy. Grinding is suitable for minor adjustments and material removal on the surface.
Sandblasting
We project fine sand particles onto the surface of the parts to increase texture and roughness. Sandblasting creates diverse surface textures for aesthetics and specific design effects.
Etching
We use chemical substances to etch the surface of the parts, creating specific patterns or textures. Etching is commonly used for marking or decorative patterns on metal parts.
Electrical Discharge Machining (EDM)
By employing electrical sparks, we create small pits and recesses on the surface of the parts, improving surface quality and increasing surface roughness.
Coating
We apply a layer of special material on the surface of the parts to provide additional protection, wear resistance, or corrosion resistance. Common coatings include chrome plating, nickel plating, and electroplating.
Anodizing
We induce an oxidation reaction on the metal surface, forming an oxide film to provide corrosion resistance and increase surface hardness. Anodizing is common for aluminum alloy parts.
Painting
We coat the surface of the parts with paint or spray paint to add color and protect the surface. Painting is widely used for both plastic and metal parts.
High Standards Quality Control for CNC Milling
We prioritize the production of your custom parts in strict compliance with rigorous manufacturing standards, ensuring adherence to the Lingshantech standard. To ensure quality, we conduct thorough verification of these requirements and include an inspection report with each order we ship.
Following the completion of the machining process, the parts can be left in their machined state or undergo post-processing as specified in the customer's requirements outlined in the purchase order (PO). This post-processing aims to enhance surface properties and achieve a visually appealing cosmetic appearance.
Our in-house quality checks are conducted before the Manufacturing Partner (MP) sends the custom parts to our facilities or their final destinations. These checks guarantee that every part adheres to the specifications outlined in the order and meets the high standards set by Lingshantech. Any requested documentation is also completed at this stage, ensuring the conformity of the parts before they are shipped out.
Lingshantech upholds a 100% commitment to quality according to ISO9001 and IATF 16949 standards. We maintain strict quality control throughout every step of the production process, from incoming quality inspection of materials to outgoing quality inspection.
We take great pride in our dedication to rigorous quality control and providing exceptional customer service. Our goal is to exceed customer expectations in all aspects of the product manufacturing process, recognizing the significant responsibility we have towards our customers.