Hey folks! Did you know that metal heat treatment goes way back, like ancient civilizations back? Yup, it’s been around for ages and has been a game-changer in tech advancements. And guess what? Today, thanks to this ancient practice, we’ve got super cool technologies making our machines churn out precise, top-notch parts. Nowadays, industries use […]
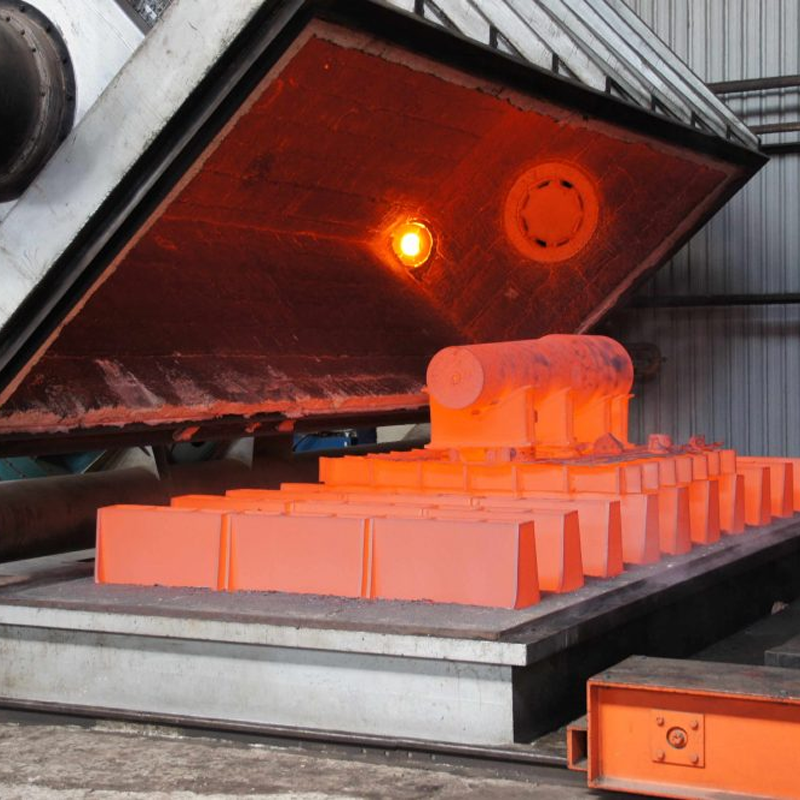